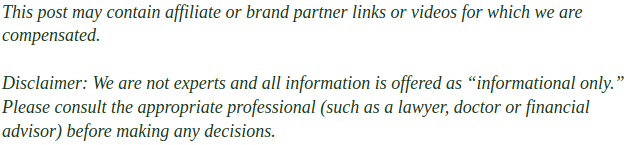

One of the best parts of owning your own business is the flexibility you have in creating products and services for your customers. There are an endless bevy of resources for you to tap into, from commercial laundry carts to plastic lockers, that can help make those seemingly lofty dreams a tangible reality. An increasingly common method of crafting custom parts is the act of rotomolding — also known as rotational molding, this highly flexible and effective method of parts production is fast becoming the go-to option for businesses large and small around the country. If you’re curious about the options at your disposal or want to learn more about this fascinating process, continue reading to get caught up!
Did You Know?
Plastic lockers and linen carts have to come from somewhere! By the beginning of 2016 the industrial laundry revenues in the United States reached an impressive $7 billion. Coin laundries, in particular, have a market worth of between $50,000 and more than $1 million — they generate $15,000 to $200,000 on a yearly basis. Rotational molding is one of the primary components in these industries reaching such unprecedented heights.
What Is Rotational Molding?
If you’re interested in crafting custom parts and products, you can’t go wrong with rotational molding. These machines come in a wide variety of different shapes and sizes to create plastic parts through heating, molding and sculpting — it gets its name from the characteristic rotation process the mold goes through to reduce the rate of unevenness and sagging that can occur during the crafting process. The Association of Rotational Moulders (shortened to ‘ARM’) is a worldwide trade association currently representing companies in nearly 60 countries.
When Was This Process Invented?
Plastic molded parts have been an integral part of modern society for decades. The very first documentation of combining rotational processes with heat and sculpting was all the way back in the mid 1800’s, rapidly growing in popularity and becoming a standard method of production in the 1900’s. Various different plastics were introduced relatively recently as awareness of their durability and safety became known, such as polyester and nylon. The two types of rotational moulding machines used by most factories are independent-arm and fixed-arm turrets — fixed-arm turret machines, in particular, use all three or four of their arms at the same time.
How Does It Work?
Rotational molding is characterized by its unique method of stretching and pressing plastic materials. During the molding process, the oven is preheated by a mixture of convection, conduction and sometimes radiation — these temperatures can reach an upwards of 500 to 700 degrees Fahrenheit depending on the polymer being used. The rotation speed itself is rather slow, generally no more than 20 rotations per minute, and is not centrifugal. During this process the timing is considered critical, as even a slight hiccup can greatly affect the end result. According to recent reports, as much as 90% of material used in rotational molding is polyethylene (also known as HPDE, LPDE and LLPDE).
Where Can I Get Started?
Creating plastic lockers, bulk containers and rolling laundry carts are all possible with the aids of rotational molding. This process has been around for many decades and is widely considered highly reliable and effective in creating many different products and parts. The average coin laundry occupies around 2,250 square feet despite having a capability of reaching 5,000 square feet total, according to the Coin Laundry Association. From laundry trucks to linen carts, nothing is out of range for rotational molding.