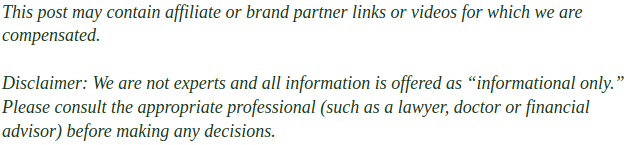

Our bridges and roads are under a lot of stress lately. Our busy world hasn’t gotten any less active over the years and, as a result, we have to contend with a lot of areas that are treacherous to cross…if they’re not out-of-order entirely. With millions of people needing to get to work or school every single day, there needs to be a happy balance between construction companies and everyday drivers. Access road construction, hydraulic shoring and temporary bridges are resources used to keep our world accessible while reducing the risk for serious accidents.
How are our roads and bridges faring? Recent statistics are suggesting they’re less-than-stellar. It’s estimated over two hundred million trips are taken daily across deficient bridges across the nation’s largest metropolitan regions. A recent survey provided by the Asphalt Pavement Alliance also sees eight out of 10 drivers saying they would much prefer road maintenance to be performed during off-peak hours. How can we make sure everyone is staying happy and safe across the board?
With over 600,000 bridges strewn across the United States and one out of every nine being considered structurally deficit, action needs to be taken as soon as possible. The Federal Highway Administration (also known as the FHWA) estimates that the country would need to invest $20 billion yearly to eliminate the bridge deficient backlog over the next decade. As of now? Only $12 billion is being spent, meaning more and more companies are looking to rent a temporary bridge as an alternative.
Oversight by OSHA is necessary to ensure each and every project is completed safely. As of now OSHA defines excavations as any man-made cut, cavity or trench in the earth’s surface. A trench, in particular, is defined as a narrow excavation made underground that is deeper than it is wide. Safe access must be provided to all excavations to ensure that even a failed project is able to be wrapped up in a timely fashion. This means ladders, ramps, steps or any other method of helping employees get in and out of the trench.
The two types of shoring available are the timber and aluminum hydraulic. Trench boxes are also used for more open areas, but they can be designated for sloping and benching. Just like shoring there are two basic types of benching available, the simple and multiple, and it all comes down to the soil to determine which one is used. Even a superior modular trench shield won’t hold fast unless it’s crafted specifically to accommodate and compliment the unique soil type the entire foundation is being built upon.
The type of soil needs to be deeply analyzed before any progress is made. Unit Weight Of Soils is a term used to refer to the weight of one unit of any particular soil type. Type A soils are what’s known as ‘cohesive soils’ and can hold up to an unconfined compressive strength of one and a half tons. These are sometimes called ‘sandy clay’, ‘clay loam’ and ‘silty clay’. Type B soils are more often called ‘angular gravel’ or ‘silt loam’. Type C soils are known as ‘sand’, ‘loamy sand’ and ‘gravel’. Each type of soil will react differently to pressure, moisture, constant movement and shifts in temperature.
All excavated soil and additional materials need to be kept at least two feet away, if not more, from trench edges to avoid an accident. A modular trench shield is needed to keep all elements separate for a seamless working environment. The bottom vertical height of a trench also isn’t allowed to exceed four feet. With the aid of a modular trench shield accidents will be significantly reduced and the quality of the finished or temporary product can be enhanced. Truss bridges are still a popular bridge design that use a diagonal mesh of posts, just flexible to be used in a number of situations.
With so much work to do and only so much time to do it, becoming acquainted with the art of the quickly assembled bridge and modular trench shield is a must.